Project Description
AUTOMATIC MONOBLOCK FOR LARGE SIZES
Aris is a fully automatic monoblock for washing sterilizing filling and capping PET or PC bottles from 3 to 6 gallons, in various models from 2 to 10 rows for productions from 300 to 3,000 bottles / hour. The bottles, previously spaced in steps from a feeding screw, are introduced into the machine through a conveyor belt and positioned in the loading area.
A harpoon system lifts and overturns them by introducing them into special pockets on the transport beams. The advancement of these beams, and therefore of the bottles, inside the machine takes place with an alternating (intermittent) movement, the speed of which is adjusted simply by acting on a timer that determines the pause / work cycle.
Automatic Size Change(Patented System)
The machine can change the size from 3 to 6 gallons without operator intervention and without replacing mechanical components. In fact, it is sufficient to choose the desired format in the display of the electrical panel and the machine adjusts itself automatically.
Penetrating Nozzles
The most important aspect of a line for recovery containers is the effectiveness of their cleaning. Our thirty years of experience has taught us that, with containers that have a body diameter much larger than the neck, it is essential to use the penetrating nozzle, it is not conceivable to correctly wash the entire internal surface of the container, and in particular of the neck, with fixed or rotating nozzles. The solution we have adopted involves a rotating multiple jet nozzle, which covers the entire internal wall of the body and neck with water, having high pressure jets directed in all directions.
Advance With Alternate Motion
The advancement of the bottles inside the machine takes place with an alternating motion; this allows to always have the nozzles aligned with the bottles in each section of the machine and, consequently, to guarantee a high washing efficiency.
Transfer System Using Centering Bushes :
In our machines the containers are inserted into special centering bushings installed step by step on the handling beams. This allows an “extremely safe” handling of the container even in the presence of a residual water inside, which is not tolerated by the machines with “gripper” handling . With our system, maintenance costs are significantly reduced, as there are no mechanical parts subject to wear.
Filling System
PROMEC has studied and implemented a filling system using electromagnetic flowmeters coupled to special filling valves, which guarantee a laminar flow without turbulence and, therefore, reduced filling times (about 8 sec. For 5 gallons) even with water at very low conductivity (up to 10 microsiemens).
External Brushing And Washing System
The external brushing of the containers takes place by means of special nylon brushes shaped so as to wrap the entire external surface of the containers, including the bottom. The effectiveness of the brushing system is guaranteed by the fact that the brushes are shaped “exactly” like the container, including the one on the bottom, and by the rotation movement of the bottle with respect to the brushes themselves; furthermore, the brushes act during one or more washing phases, in which the bottle holder beams are not in motion, since the motion of the machine is alternating and therefore the action time of the brushes is decidedly higher than in continuous motion machines. In the brushing area, as well as in other sections of the machine, there are manifolds for the pressure washing of the external surface of the bottles.
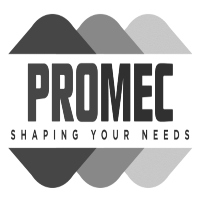